
DORADZTWO

TESTOWANIE

ROZWÓJ
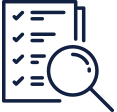
BADANIA
Analiza materiałów i awarii
Material degradation: Cracking, Corrosion, Stress Corrosion Cracking, Wear and more
The team of microstructural characterisation possesses a profound knowledge and professional experience in the field of material development and optimization, failure analysis and quality control. We are working in close contact with ESA, the aerospace industry and corresponding research institutes on a huge variety of metals and alloys like, in particular, steels, Al- and Ti-alloys, composites, coatings and electronic materials. A significant part of our work has been devoted to failure analysis which requires mechanical-, corrosion- or tribological phenomena to be understood and correlated with production processes and application environments. Our motivated team works constantly on widening the preparation and analysis methods in order to be able to resolve even the most challenging failures and damage cases.
Failure analysis is used to determine the causes of component failures. Various analytical techniques are employed to investigate the damage and to identify the primary cause, which often leads to further damages that are merely consequential. Only by identifying this so-called root cause remedial measures can be derived. Thus, our approach at AAC is not only to image the failure but also to provide inputs for a possible optimisation of materials and components.
As an independent laboratory, we provide comprehensive failure analysis to our customers as a service. Failure analysis may include the following:
- Analysis of broken parts and components
- Assessment of cracks
- Quantitative measurement of wear rates
- Assessment of corrosion
- Interpretation of deposits on functional surfaces
- Detection of inclusions and defects that may influence mechanical properties…
Why failure analysis?
The purpose of a failure analysis is the systematic in-depth identification of the causes of component failures. The goal is to understand the root-cause damage to take appropriate measures for remediation and future prevention. Component failures typically lead to economic losses (production downtime, consequential damages, recalls, etc.) and possibly endangers human health. Clarifying technical damages and their causes is a crucial prerequisite for damage prevention. Thus, damage analysis is an indispensable part of learning from failures.
When considering failure analysis, the following points must be taken into account:
- Root Cause Identification: Failure analysis helps identify the underlying causes of damage. This enables targeted treatment of the primary cause of the problem.
- Prevention of Consequential Failures: Early detection and correction of damages often prevents further damages.
- Derivation of Remedial Measures: Based on the findings of a failure analysis, measures can be derived to prevent future damages.
- Improvement of processes, materials, and components: By analysing damages, weaknesses in processes or components can be identified and the compatibility of materials is assessed. This allows corrective measures and the that will improve efficiency and reliability of processes and components.
What can AAC offer?
- Comprehensive failure analysis: Our systematic failure analyses do not stop at examining superficial damages. We perform in-depth investigations to determine the underlying causes.
- Expert expertise: Our experienced team of experts employs various analytical methods to investigate a wide range of different failure cases.
- Informative report: Our customers receive a comprehensive report with interpretations and conclusions from which action plans can be derived.
- Customer-oriented approach: Each assignment is individual, and therefore our analyses are tailored to the specific customer requirements.
Methods of Failure Analysis offered by AAC
- Mikroskopia świetlna
Za pomocą różnych nowoczesnych mikroskopów świetlnych (mikroskopii stereoskopowej i mikroskopii światła odbitego) można szczegółowo wyświetlać struktury powierzchni. Obejmuje to między innymi analizę powierzchni pęknięć, badania metalograficzne, pomiary grubości warstw w przekrojach poprzecznych i wiele innych.
- Surface Analysis:
Surfaces are investigated using optical methods to determine the roughness, waviness and flatness of a surface. On the one hand, certain structures (e.g. peaks, valleys, grooves, pores, particle adhesions, etc.) can be measured and, on the other hand, the surface can be quantitatively characterized (determination of Ra, Rz and other statistical surface characteristics). The quantitative parameters are determined from 2D profile measurements and 3D surface measurements.
As an alternative to using purely optical methods, it is also possible to generate a digital surface model from SEM images using complex software programs and to derive the above-mentioned surface parameters from this model. This enables the assessment of waviness and roughness as well as the measurement of structures even on surfaces that are not accessible to optical inspection (e.g. measurement of microscopic features on a surface).
- Mikroskopia elektronowa:
Badania obrazowe o wysokiej rozdzielczości próbek materiałów i komponentów są przeprowadzane przy użyciu skaningowej mikroskopii elektronowej (SEM). Zastosowanie różnych detektorów dostarcza różnych informacji o strukturze badanej powierzchni: topografia może być najlepiej obrazowana za pomocą elektronów wtórnych (detektor SE), podczas gdy elektrony rozproszone wstecznie (detektor BSE) są wykorzystywane do obrazów kontrastu materiału. Detektor umieszczony w obiektywie umożliwia uzyskanie obrazów o wysokiej rozdzielczości z rozdzielczością w zakresie nm.
Co więcej, powierzchnia próbki może być przetwarzana in-situ w skali poniżej µm za pomocą zogniskowanej wiązki jonów (FIB) w celu zbadania obszaru bezpośrednio pod powierzchnią. Jest to wykorzystywane na przykład do analizy struktur warstwowych lub analizy uszkodzeń. Obrazowanie próbki za pomocą wiązki jonów umożliwia również wyświetlenie struktury ziaren w wysokim kontraście.
SEM są również wyposażone w nowoczesne systemy EDX umożliwiające analizę chemiczną badanej powierzchni (lub w sekcji FIB). Bardziej złożone zagadnienia można badać za pomocą skanów liniowych, które pokazują przebieg koncentracji wybranych pierwiastków.
Aby szczegółowo zbadać strukturę krystaliczną materiału, dostępna jest dyfrakcja elektronów z rozproszeniem wstecznym (EBSD). Dzięki tej nowoczesnej metodzie mikrostruktury mogą być badane z wysoką rozdzielczością boczną w celu określenia następujących cech: identyfikacja poszczególnych faz, badanie granic ziaren, różnice w orientacji sąsiednich ziaren, identyfikacja osadów itp.
- Metallography:
Badania metalograficzne służą do jakościowego i ilościowego opisu struktury materiałów przy użyciu metod mikroskopowych. W przypadku analiz metalograficznych, przekroje poprzeczne są przygotowywane przy użyciu zaawansowanych procedur przygotowawczych (takich jak mechaniczne, elektrochemiczne, chemiczne). Mikrostruktury są następnie badane na tych przekrojach za pomocą mikroskopii świetlnej lub skaningowej mikroskopii elektronowej i określane są takie cechy, jak proporcje faz, rozmiary ziaren, rozkład wielkości ziaren, rozmiary cząstek i wytrącenia. Pozwala nam to zapewnić dogłębną analizę materiałów i umożliwia wysokiej jakości analizę uszkodzeń i pęknięć.
- (Micro)Hardness measurements:
The hardness of metals, non-metals and coatings is determined by penetration tests: Hardness is defined as the resistance to penetration of a test specimen; the size of the permanent imprint of the test specimen serves as the measurement variable (Vickers, Knoop or Brinell method).
To determine the hardening depth, surface hardness depth and nitriding hardness depth of surface hardened steels, a series of hardness indentations are placed on the polished cross section from the sample edge towards the sample centre. The corresponding hardness depths are derived from the hardness-depth curve determined in this way.
Modern state-of-the-art equipment available at AAC enables the (fully automated) investigation of hardness with loads in the range of 0,25 g – 62,5 kg. Furthermore, harness mappings (e.g., line-scans, matrix-scans) can be performed to assess the lateral distribution of mechanical properties.