
CONSULTING

TESTING

DEVELOPMENT
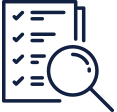
RESEARCH
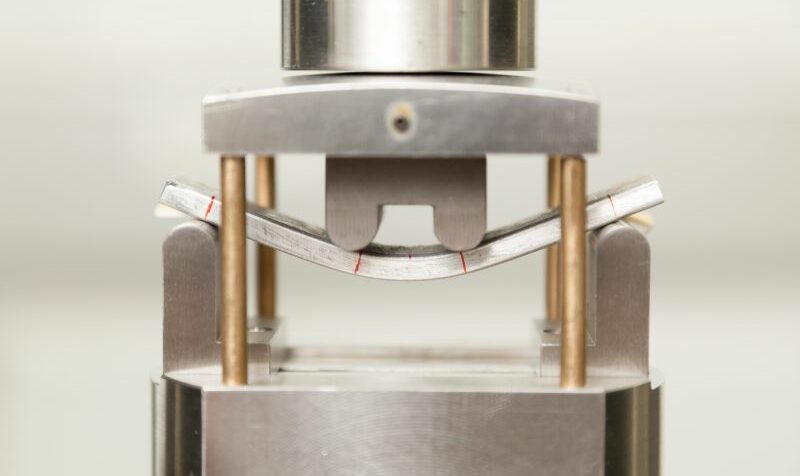
Surface Characterization
Precise analyis and tests
Static Contact Angle measurement
Static contact angle measurement is a fundamental technique used to determine the wetting properties of a surface. It involves placing a droplet of liquid on a solid substrate and measuring the angle formed at the liquid-solid interface. This angle, known as the contact angle, provides insights into the surface energy of the solid and the interfacial tension between the liquid and the solid. A high contact angle indicates low wettability, suggesting a hydrophobic surface, while a low contact angle indicates high wettability, suggesting a hydrophilic surface. Static contact angle measurements are essential in evaluating surface treatments, coatings, and cleanliness of materials.
Roll-off angle measurement
Roll-off angle measurement, also known as the sliding angle or tilt angle, complements static contact angle analysis by assessing the mobility of a droplet on a tilted surface. In this method, a surface is gradually tilted until the droplet begins to move, and the angle at which this occurs is recorded as the roll-off angle. This measurement provides additional information about the dynamic wetting behavior and adhesion properties of the surface. Low roll-off angles indicate that the surface has low adhesion and the liquid droplets can easily slide off, which is desirable in applications requiring self-cleaning or anti-icing properties. Together, static contact angle and roll-off angle measurements offer a comprehensive understanding of surface characteristics and their practical implications in various applications.
Surface Energy Determination
Knowledge of surface energy is an important prerequisite for understanding and influencing interfacial phenomena in various scientific and industrial application. Surface energy is determined by the contact angle measurement of a liquid drop on a solid surface. The surface energy of solids influences their wetting behavior, adhesion, and compatibility with other materials, playing an essential role in the development and evaluation of coatings and adhesives.
Surface Tension Determination
Surface tension of liquids determines their spread and droplet formation and has a significant impact on processes such as emulsification and foam formation. It is also used in applications like inkjet printing. Surface tension is measured by the contact angle of a liquid drop, providing insights into how liquids interact with surfaces and other liquids. Understanding surface tension is crucial for optimizing various industrial processes and improving product performance.
Static ice shear adhesion
A quick and simple laboratory method for determining ice adhesion is important for the development of anti-ice coatings. The laboratory method developed by AAC uses a non-impact ice push test that can quickly determine the shear-force of ice adhesion to a coating in the range of 10 kPa to 1 MPa.
Adhesion and scratch hardness tests
Adhesion testing is used to determine, on the one hand, the adhesion strength between the coating and the substrate and, on the other hand, the internal cohesion of a coating system (e.g. a multi-layer structure). For this purpose, cross-cutting tests and scratch hardness tests are carried out.