
CONSULTING

TESTING

DEVELOPMENT
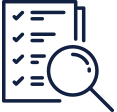
RESEARCH
Lubrication for Space
Development of self-lubricating materials. Coatings and lubrication concepts for space
Lubrication in space is extremely different from terrestrial conditions. Even the lack of air (vacuum) prevents the use of common terrestrial solutions: Lubricants evaporate, materials age (polymers) or are not corrosion resistant (nitriding steels), most metallic alloys tend to extremely high galling (adhesive wear) in vacuum or cold welding under vibrations during launch, many coatings suddenly show high friction (DLC). The choice of materials, surface processes and lubrication cannot be taken from conventional terrestrial solutions.
Increasing demands are put on mechanisms, e.g. due to demands on contamination fluid lubricants may be banned, longer life needs to improve wear resistance of the materials themselves by surface treatments, or low temperatures may need to adopt fluid lubricants or develop new solid lubrication or derive combined / hybrid lubrication concepts.
Increasing requirements like mass reduction with simultaneous increase of mechanism performance, require continuously further developments. AAC observes the trends and tries to identify new niche products. Together with industrial manufacturers and/or end-users, AAC assists in the development of new solution concepts, followed by prototype testing on our specialized equipment up to qualification. AAC, with its history as R&D department, also offers the coordination of development projects.
In the development of a self-lubricating polymer for cages in ball bearings, AAC provides coordination, material design and testing from the material to the ball bearings. The material is then offered commercially by the manufacturer. In addition, AAC led the development of a hybrid lubrication concept for gears that enables high efficiency down to low temperatures. A new nitriding process for PH steels was validated in combination with a composite MoS2 coating to maintain this high efficiency over a long service life. AAC also assists in development of new fluid lubricants as e.g. ionic liquids. All these measures finally reduce the mass and electrical power of the motor.