
CONSULTING

TESTING

DEVELOPMENT
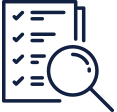
RESEARCH
Simulation
FEM, mechanical, thermal and infusion process simulation, smart materials
Simulation is a very important step in the design, manufacturing and behavior of parts and assemblies working under various different environmental conditions. AAC provides static and transient thermal, structural and multi-physical Finite Element simulations such as thermal behavior of mechanisms working in space environment, mechanical and damage behavior of composite structures or the behavior of smart materials like shape memory alloys or piezo materials. For the design and production of composite parts by resin infusion AAC offers finite element simulation-based information on the draping and infiltration behavior of dry preforms, deformation of parts after demolding (spring-in) and the thermo-mechanical behavior of molds to predict the heating behavior and deformation under pressure.