
CONSULTING

TESTING

DEVELOPMENT
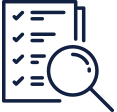
RESEARCH
Material & Failure Analysis
Material degradation: Cracking, Corrosion, Stress Corrosion Cracking, Wear and more
The team of microstructural characterisation possesses a profound knowledge and professional experience in the field of material development and optimization, failure analysis and quality control. We are working in close contact with ESA, the aerospace industry and corresponding research institutes on a huge variety of metals and alloys like, in particular, steels, Al- and Ti-alloys, composites, coatings and electronic materials. A significant part of our work has been devoted to failure analysis which requires mechanical-, corrosion- or tribological phenomena to be understood and correlated with production processes and application environments. Our motivated team works constantly on widening the preparation and analysis methods in order to be able to resolve even the most challenging failures and damage cases.
Failure analysis is used to determine the causes of component failures. Various analytical techniques are employed to investigate the damage and to identify the primary cause, which often leads to further damages that are merely consequential. Only by identifying this so-called root cause remedial measures can be derived. Thus, our approach at AAC is not only to image the failure but also to provide inputs for a possible optimisation of materials and components.
As an independent laboratory, we provide comprehensive failure analysis to our customers as a service. Failure analysis may include the following:
- Analysis of broken parts and components
- Assessment of cracks
- Quantitative measurement of wear rates
- Assessment of corrosion
- Interpretation of deposits on functional surfaces
- Detection of inclusions and defects that may influence mechanical properties…
Why failure analysis?
The purpose of a failure analysis is the systematic in-depth identification of the causes of component failures. The goal is to understand the root-cause damage to take appropriate measures for remediation and future prevention. Component failures typically lead to economic losses (production downtime, consequential damages, recalls, etc.) and possibly endangers human health. Clarifying technical damages and their causes is a crucial prerequisite for damage prevention. Thus, damage analysis is an indispensable part of learning from failures.
When considering failure analysis, the following points must be taken into account:
- Root Cause Identification: Failure analysis helps identify the underlying causes of damage. This enables targeted treatment of the primary cause of the problem.
- Prevention of Consequential Failures: Early detection and correction of damages often prevents further damages.
- Derivation of Remedial Measures: Based on the findings of a failure analysis, measures can be derived to prevent future damages.
- Improvement of processes, materials, and components: By analysing damages, weaknesses in processes or components can be identified and the compatibility of materials is assessed. This allows corrective measures and the that will improve efficiency and reliability of processes and components.
What can AAC offer?
- Comprehensive failure analysis: Our systematic failure analyses do not stop at examining superficial damages. We perform in-depth investigations to determine the underlying causes.
- Expert expertise: Our experienced team of experts employs various analytical methods to investigate a wide range of different failure cases.
- Informative report: Our customers receive a comprehensive report with interpretations and conclusions from which action plans can be derived.
- Customer-oriented approach: Each assignment is individual, and therefore our analyses are tailored to the specific customer requirements.
Methods of Failure Analysis offered by AAC
- Light microscopy
With the help of various modern light microscopes (stereo and reflected light microscopy), surface structures can be displayed in detail. These include, among other things, the analysis of fracture surfaces, metallographic examinations, measurement of layer thicknesses in cross sections, and much more.
- Surface Analysis:
Surfaces are investigated using optical methods to determine the roughness, waviness and flatness of a surface. On the one hand, certain structures (e.g. peaks, valleys, grooves, pores, particle adhesions, etc.) can be measured and, on the other hand, the surface can be quantitatively characterized (determination of Ra, Rz and other statistical surface characteristics). The quantitative parameters are determined from 2D profile measurements and 3D surface measurements.
As an alternative to using purely optical methods, it is also possible to generate a digital surface model from SEM images using complex software programs and to derive the above-mentioned surface parameters from this model. This enables the assessment of waviness and roughness as well as the measurement of structures even on surfaces that are not accessible to optical inspection (e.g. measurement of microscopic features on a surface).
- Electron Microscopy:
High-resolution imaging examinations of material samples and components are carried out using scanning electron microscopy (SEM). The use of different detectors provides different information about the structure of the surface being examined: the topography can best be imaged with secondary electrons (SE detector), while backscattered electrons (BSE detector) are used for material contrast images. An in-lens detector enables high-resolution images with resolutions down to the nm range.
Furthermore, the sample surface can be processed in-situ on a sub-µm scale using a focused ion beam (FIB) to examine the area immediately below the surface. This is used, for example, to analyse layer structures or in failure analysis. Imaging the sample using an ion beam also enables the grain structure to be displayed in high contrast.
The SEMs are also equipped with modern EDX systems to enable chemical analysis of the examined surface (or in the FIB section). More complex questions can be investigated using line scans, which show the concentration course for selected elements.
To examine the crystalline structure of a material in detail, electron backscatter diffraction (EBSD) is available. With this modern method, microstructures can be examined with high lateral resolution to determine the following characteristics: identification of individual phases, examination of grain boundaries, differences in orientation of neighbouring grains, identification of precipitates, etc.
- Metallography:
Metallographic investigations serve to describe the structure of materials qualitatively and quantitatively using microscopic methods. For metallographic analyses, cross-sections are prepared using advanced preparation procedures (such as mechanical, electrochemical, chemical). The microstructures are then examined on these cross sections using light microscopy or scanning electron microscopy and characteristics such as phase proportions, grain sizes, grain size distribution, particle sizes and precipitates are determined. This allows us to provide in-depth analysis of materials and enables high-quality failure and fracture analysis.
- (Micro)Hardness measurements:
The hardness of metals, non-metals and coatings is determined by penetration tests: Hardness is defined as the resistance to penetration of a test specimen; the size of the permanent imprint of the test specimen serves as the measurement variable (Vickers, Knoop or Brinell method).
To determine the hardening depth, surface hardness depth and nitriding hardness depth of surface hardened steels, a series of hardness indentations are placed on the polished cross section from the sample edge towards the sample centre. The corresponding hardness depths are derived from the hardness-depth curve determined in this way.
Modern state-of-the-art equipment available at AAC enables the (fully automated) investigation of hardness with loads in the range of 0,25 g – 62,5 kg. Furthermore, harness mappings (e.g., line-scans, matrix-scans) can be performed to assess the lateral distribution of mechanical properties.